This article discusses in depth the two main processes in the production of polyethylene film – blow molding and cast film. It introduces in detail the advantages of polyethylene blow molding process in terms of simple equipment, good film performance and product diversity, as well as the characteristics of polyethylene cast film process in terms of uniform thickness, fast production speed and high transparency. At the same time, the shortcomings of the two processes in terms of thickness uniformity, production speed, equipment complexity, etc. are analyzed, and process recommendations for different application scenarios are given.
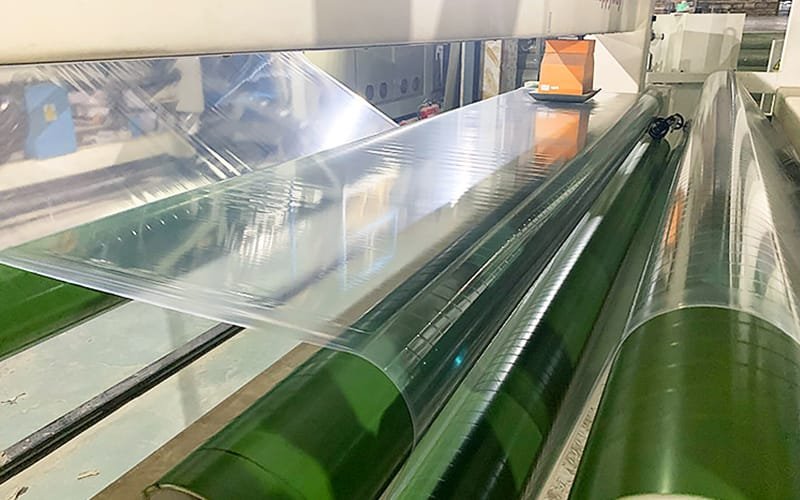
I. Introduction
Polyethylene film has been widely used in the packaging field due to its good flexibility, heat resistance, moisture and water resistance, oxidation resistance and high transparency. In the production process of polyethylene film, blow molding process and cast film process are the two main production methods. This article will discuss in detail the differences between the two processes in order to better understand and select the appropriate production process.
II. Excellent characteristics of polyethylene film blow molding process
- Simple equipment
The equipment of polyethylene blow molding process is relatively simple, mainly including extruder, blowing device, traction device and winding device. This simple equipment structure makes the investment cost of the blow molding process low, which is suitable for small and medium-sized enterprises or enterprises with limited funds.
- Good film performance
The polyethylene film produced by the blow molding process has good tensile properties and toughness. During the blowing process, the film is stretched in both the longitudinal and transverse directions, so that the molecular chains are oriented and arranged, thereby improving the mechanical properties of the film. This property makes the blown film suitable for packaging purposes with high strength requirements, such as polyethylene packaging bags.
- Product diversity
The blow molding process can produce polyethylene films of various specifications, such as the width and thickness of the film, which can be easily adjusted. In addition, by changing the process parameters such as the blowing ratio, films with different properties and uses can also be produced, such as thicker films for agricultural covering or thinner films for food packaging.
III. Excellent characteristics of polyethylene film casting process
- Uniform thickness
The polyethylene film produced by the casting process has very good thickness uniformity. During the casting process, the polymer melt is extruded through a flat die head and quickly cooled on a cooling roller to form a film. This molding method makes the thickness distribution of the film in the width direction relatively uniform, and the thickness of the film can be accurately controlled. This high-precision thickness control makes cast film have significant advantages in application scenarios such as electronic packaging that require high thickness accuracy.
- Fast production speed
The cast process has a high production speed and can achieve large-scale and efficient production. Since the cast process is relatively simple and smooth, the melt can be quickly cooled and shaped after extrusion, and production can be carried out continuously, so more polyethylene film products can be produced per unit time.
- High transparency
The polyethylene film produced by the cast process has high transparency and good gloss. This is because during the cast production process, the film cools quickly, resulting in relatively low crystallinity and a more regular arrangement of molecular chains, thereby reducing the scattering of light. This high-transparency film is suitable for products that require high-transparency packaging, such as polyethylene packaging films for food, daily necessities, etc.
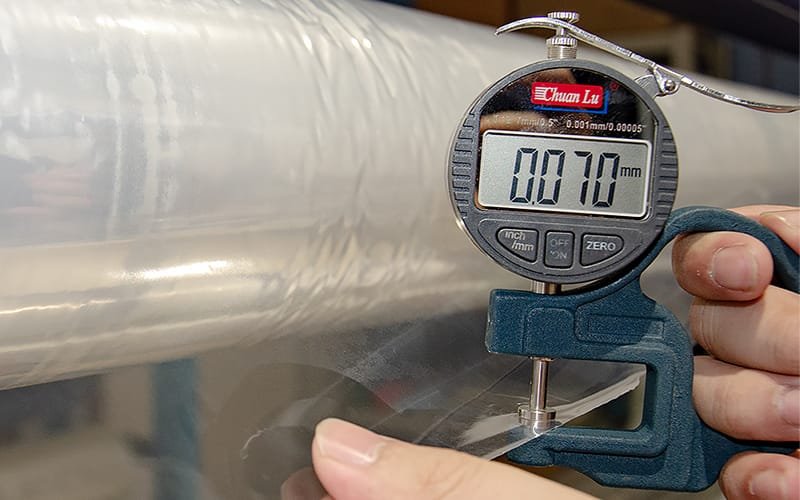
IV. Deficiencies and comparison between blow molding and cast molding processes
- Deficiencies of blow molding process
Although the blow molding process has the advantages of simple equipment, good film performance and product diversity, it also has some deficiencies. First, the film produced by the blow molding method has a slightly poor thickness uniformity. Affected by various factors such as air flow and cooling speed, the thickness of the film in the circumferential direction may fluctuate. Secondly, the production speed of the blow molding method is relatively slow, because the blow molding process includes multiple links such as inflation and cooling, and the speed of each link is limited.
- Disadvantages of the cast film process
Although the cast film process has the advantages of uniform thickness, fast production speed and high transparency, it also has problems such as complex equipment and high investment cost. The equipment of the cast film method is relatively complex, requiring high-precision extruders, special cast film dies and cooling rollers and other components, and the maintenance and operation of these equipment require a high level of technology.
- Comparison and recommendation
When comparing the two processes, it can be seen that the blow molding process is more suitable for enterprises with high requirements for film strength, loose requirements for thickness uniformity and limited funds; while the cast film process is more suitable for enterprises with high requirements for film thickness uniformity, transparency and production speed. Therefore, when choosing a production process, enterprises should make comprehensive considerations based on their own product needs, financial conditions and technical levels.
For products with high strength requirements such as polyethylene packaging bags, the blow molding process is a good choice. For electronic packaging or food packaging films that require high transparency and high-precision thickness control, the cast film process is more advantageous.
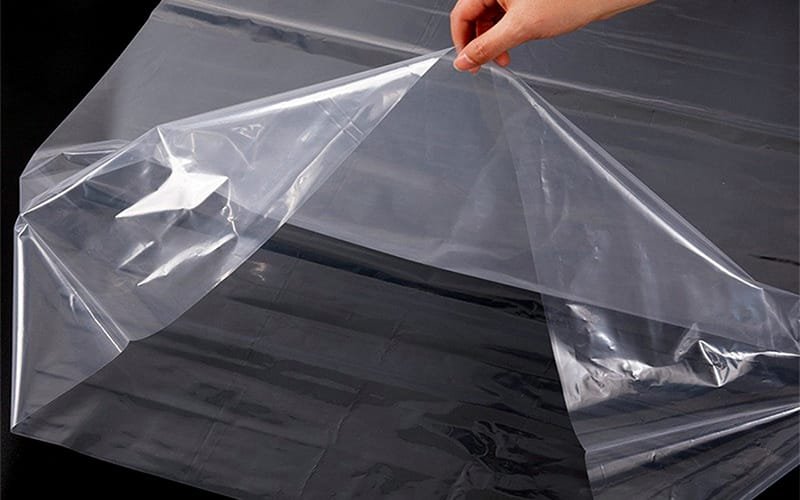
V. Conclusion
The blow molding process and cast film process of polyethylene film each have their own advantages and disadvantages and are suitable for different application scenarios. The blow molding process is widely used in the fields of polyethylene packaging bags due to its simple equipment, good film performance and product diversity; while the cast film process occupies an important position in the fields of electronic packaging and food packaging films due to its advantages such as uniform thickness, fast production speed and high transparency. When choosing a production process, enterprises should make comprehensive considerations based on their own needs to achieve the best economic benefits and product quality.